SERVICES
SATEL Injection Moulding Department offers a wide range of different services
- production of plastic components on injection moulding machines, using our own and customer provided moulds
- manufacture of two-component parts
- production of elements in the insert moulding technology
- production of moulded parts in the HEAT AND COOL technology
- overprinting
- packing of manufactured parts
- assembly of finished products from manufactured and/or delivered components
- delivery of parts to a specified address
We process the following materials:
PC, PS, ABS, SAN, PP, PE, PA, PBT, including glass fibre reinforced plastics up to 50%.
Two-component injection moulding
Two-component injection moulding is an advanced plastic processing technology used to manufacture complex parts from two different types of plastics in a single process. For example: parts with a gasket function, which are a combination of hard plastic and thermoelastomer. It is just one example of the most frequently made two-component combination.
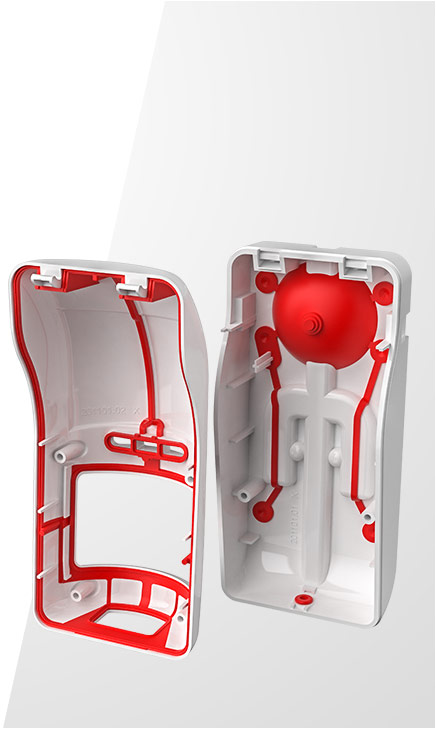
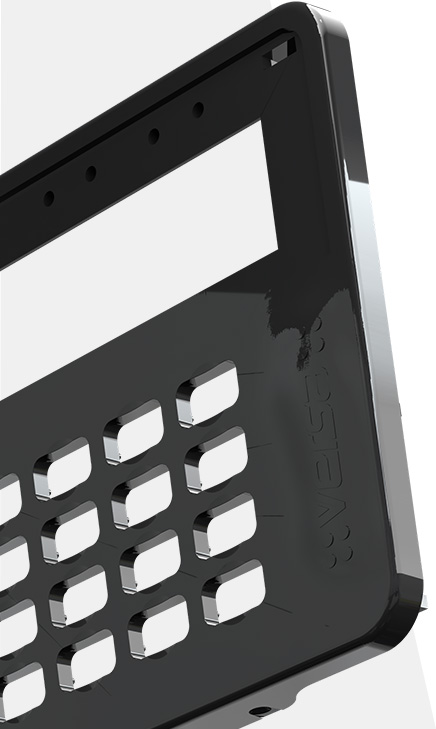
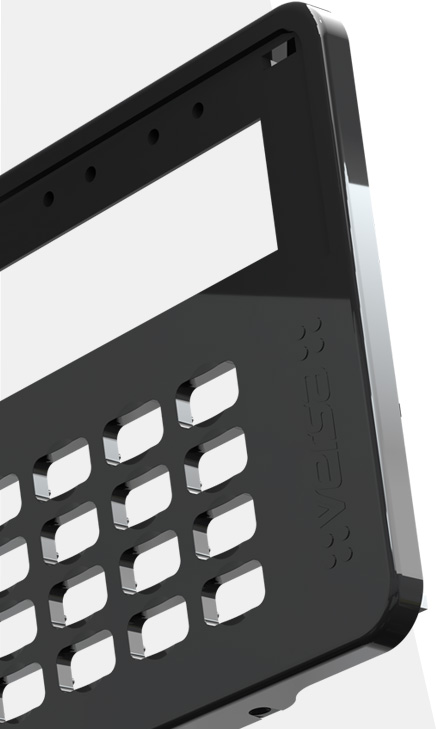
HEAT AND COOL
Technology
SINGLE ATT (Alternating Temperature Technology) is used to introduce temperature changes with a difference of more than 100°C. As the system fills moulds alternately with warm and cold thermal fluids, it can actively heat or cool processes in defined alternation.
The alternating temperature control of the tool provides a number of benefits in the production of moulds, for example improves mould surfaces and strength as well as increases the economic efficiency of the process.
The alternating temperature control of the tool provides a number of benefits in the production of moulds, for example improves mould surfaces and strength as well as increases the economic efficiency of the process.
- maintains pressure for longer (also in areas remote from the pouring point) and reduces the need for injection pressure and clamping force
- supports the creation of surface effects, e.g. self-cleaning or anti-glare finish, helps shape the micro- and nano-structure of the moulds and creates particularly smooth, high-quality gloss surfaces with a piano lacquer appearance
- ensures a more homogeneous arrangement of the glass fibres in technical parts
- extends the time of the molten material front surfaces welding and reduces the number of weld seam marks on the surface of injection moulded parts
- reduces the risk of warping due to shrinkage, thus improving dimensional accuracy and consistency of injection parameters
- reduces cycle time
Insert moulding and overmoulding
The insert moulding technology makes it possible to achieve a strong and secure plastic-metal bond. The use of inserts – e.g. threaded bushings – improves the functional properties of moulded parts, thus increasing their mechanical resistance and durability.
Our Injection Moulding Department uses an automated production cell, equipped with a vibrating insert feeder and a multi-axis robot. This allows the production of even the most complex elements.
Our Injection Moulding Department uses an automated production cell, equipped with a vibrating insert feeder and a multi-axis robot. This allows the production of even the most complex elements.
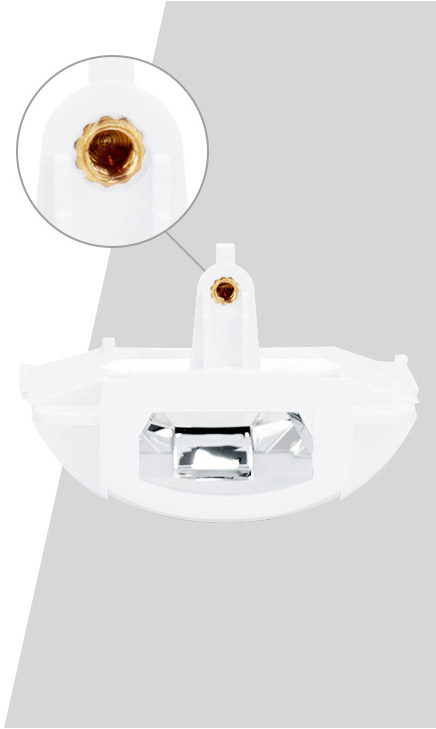